Best Guide to Preventing Weld Undercut: Tips and Techniques
Wiki Article
Understanding the Art of Welding: How to Prevent Undercut Welding Issues for Flawless Fabrication Outcomes
By understanding the root triggers of undercut welding and implementing efficient techniques to prevent it, welders can elevate their craft to brand-new levels of excellence. In the search of perfect fabrication results, understanding the art of welding to prevent undercut problems is not just a skill yet a need for those striving for excellence in their job.Comprehending Undercut Welding
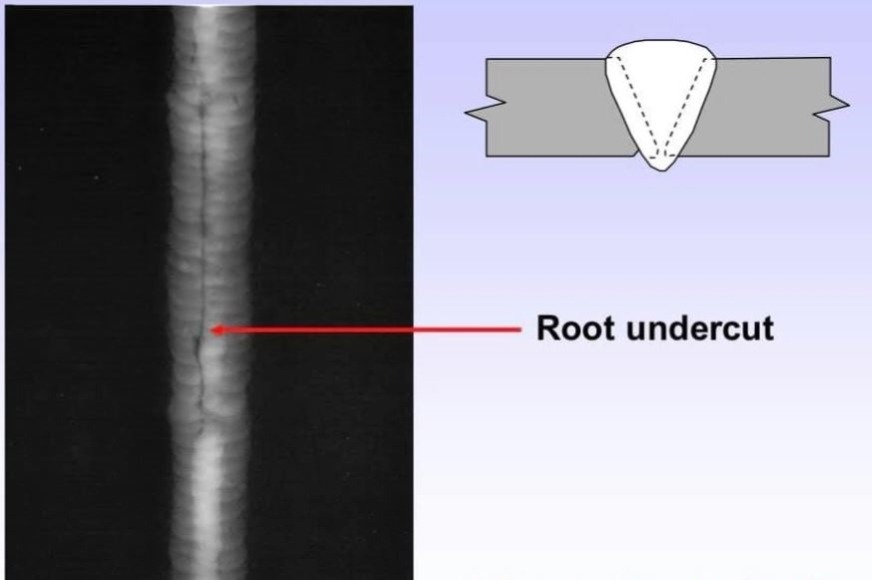
To avoid undercut welding, welders ought to make certain proper welding criteria, such as readjusting the existing, voltage, traveling rate, and preserving the right electrode angle. By understanding the reasons of undercut welding and carrying out precautionary measures, welders can attain high-quality, structurally audio welds.
Root Causes Of Undercut in Welding
Comprehending the elements that add to damage in welding is vital for welders to create high-quality, structurally sound welds. Insufficient welding existing or wrong welding speed can also contribute to undercut. Understanding these causes and applying appropriate welding techniques can aid protect against undercutting concerns, making sure solid and sturdy welds.Methods to avoid Undercutting

To reduce the danger of undercutting in welding, welders can utilize strategic welding strategies intended at improving the quality and honesty of the weld joints. Furthermore, using the correct welding technique for the details joint setup, such as weave or stringer grains, can add to decreasing damaging.
Using back-step welding techniques and controlling the weld grain account can additionally help distribute heat evenly and decrease the risk of undercut. Normal evaluation of the weld joint during and after welding, as well as executing high quality guarantee steps, can help in discovering and dealing with damaging issues promptly.
Importance of Correct Welding Specifications
Selecting and maintaining appropriate welding parameters is essential for attaining successful welds with very little issues. Welding criteria describe variables such as voltage, existing, travel rate, electrode angle, and protecting gas flow rate that directly affect the welding procedure. These criteria have to be meticulously changed based on the sort of material being welded, its thickness, and the welding technique utilized.Correct welding parameters ensure the correct amount of heat is put on melt the base steels and filler material uniformly. If the parameters are established expensive, it can cause too much warm input, creating over at this website burn-through, distortion, or spatter. On the various other hand, if the specifications are also reduced, insufficient fusion, absence of penetration, or undercutting might take place.
Top Quality Assurance in Welding Procedures

Verdict
To conclude, grasping the art of welding needs a complete understanding of undercut welding, its reasons, and techniques to stop it. By making sure proper welding criteria and carrying out quality control methods, flawless fabrication outcomes can be attained. It is crucial for welders to constantly pursue excellence in their welding operations to prevent undercut concerns and produce high-quality welds.Undercut welding, an usual problem in welding procedures, takes place when the weld steel doesn't correctly fill the groove and leaves a groove or depression along the bonded joint.To protect against undercut welding, welders ought to ensure go to website appropriate welding criteria, such as readjusting the current, voltage, traveling speed, and keeping the correct electrode angle. Poor welding incorrect or present welding speed can also add to undercut.To reduce the threat of undercutting in welding, welders can use critical welding techniques intended at boosting the high quality and honesty of the weld joints.In verdict, mastering the art of welding calls for a comprehensive understanding of undercut welding, its causes, and strategies to avoid it.
Report this wiki page